AI Industrial Vehicle Automation
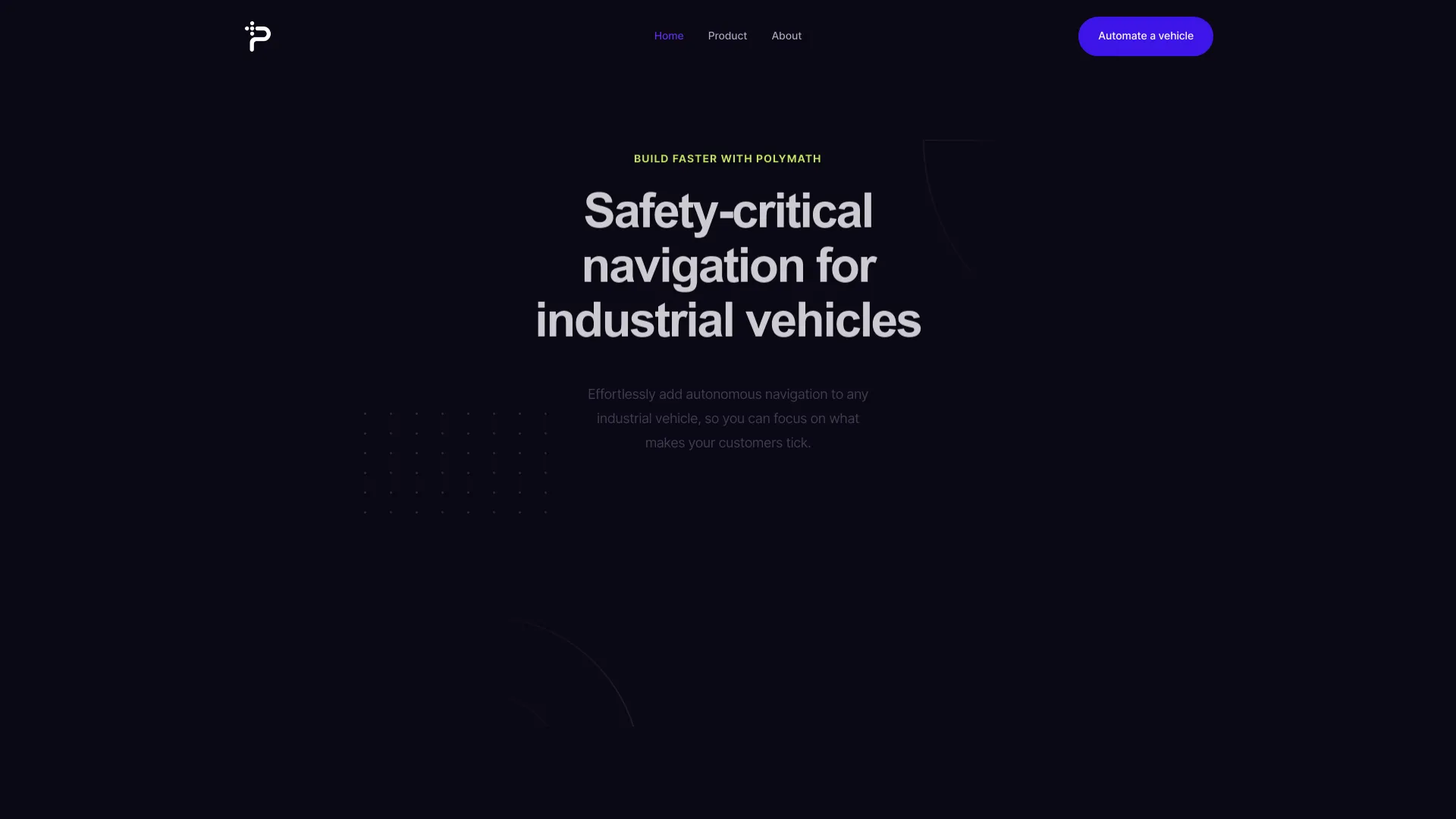
What is polymathrobotics.com?
Polymath Robotics specializes in automating industrial vehicles, offering a vehicle-agnostic technology adaptable to various vehicles like agricultural equipment and mining machinery. Their system is commandable through an API, ensuring compatibility with most sensors and aiming to streamline the integration of autonomy into industrial vehicles, reducing implementation time significantly.
Founded by robotics and autonomy experts and backed by industry leaders, the company emphasizes critical autonomy components such as path planning, hazard detection, behavior trees, human detection, controls tuning, and safety.
Noteworthy features include easy installation, a mature vehicle dynamics model, minimal field service requirements, and low network bandwidth usage, highlighted by satisfied customers. Additional information can be found on their official website or About page.
How do I integrate my existing sensor with the system of polymathrobotics.com?
To integrate your existing sensor with Polymath Robotics' system, follow these steps:
Ensure Compatibility: Confirm that your sensor has a LINUX driver, as Polymath's system is compatible with sensors operating on LINUX.
Understand the Perception System: Familiarize yourself with how Polymath's object detection system functions. It processes lidar point clouds, employing algorithms like Patchwork++ for ground segmentation and height-based filtering to identify obstacles.
Contact Polymath Robotics: Directly reach out to Polymath Robotics for integration guidance. Their team can offer specific instructions and support tailored to integrating your sensor with their system.
API Commands: Utilize Polymath's API to send commands to the system. This API facilitates seamless communication between your sensor and Polymath's autonomy modules.
Testing and Tuning: Post-integration, conduct thorough testing to ensure the system accurately interprets sensor data. You may need to fine-tune the system to optimize its performance for your particular use case.
For comprehensive instructions and assistance, consulting Polymath Robotics' technical team directly is recommended.
What are the benefits of polymathrobotics.com?
The advantages of adopting Polymath Robotics' system include:
Vehicle-Agnostic: The technology is adaptable to a wide array of industrial vehicles, offering versatility across different sectors.
Sensor Compatibility: Supporting most sensors with LINUX drivers, it allows for flexible integration with various sensor types.
API Command Capability: With the ability to be commanded via an API, the system enables straightforward communication and control.
Efficiency: Significantly reduces the time needed to implement vehicle autonomy, streamlining the process from months to weeks.
Ease of Installation: Customers highlight the system's simplicity in installation and minimal requirement for field service deployments.
Operational Optimization: Facilitates operational optimization, empowering businesses to enhance productivity levels.
Safety-Critical Navigation: Provides safety-critical navigation, ensuring the autonomous operation is secure.
Effortless Autonomy: Designed for seamless autonomy, simplifying the automation process for users.
In specific industries, these benefits are further pronounced:
- Construction: Automation of repetitive tasks leads to improved efficiency.
- Agriculture: Enables autonomous navigation and precision farming techniques.
- Transportation: Enhances safety and diminishes the necessity for manual intervention.
These advantages position Polymath Robotics as a cost-effective and efficient solution for automating industrial vehicles across diverse sectors.
What are the limitations of polymathrobotics.com?
When evaluating Polymath Robotics' system, it's essential to consider potential limitations:
Industrial Focus: Tailored for industrial vehicles in controlled environments, the system may not be suitable for applications requiring navigation in urban or public spaces.
Vehicle Requirements: Specific vehicle criteria, such as Ackermann or differential steering, are necessary for compatibility. Vehicles not meeting these requirements may not integrate with Polymath's system.
Size and Efficiency: While capable of automating larger and less fuel-efficient vehicles, the system does not address inherent size, cost, or fuel efficiency issues prevalent in certain industries.
Development Stage: Polymath Robotics is in its early stages, offering a complete simulation environment for development. Some features may still be in development or refinement, affecting the system's readiness for certain applications.
Hardware Dependencies: While software is hardware-agnostic, actual vehicle automation necessitates compatible hardware, potentially requiring additional investments or partnerships with hardware providers.
Complexity in Robotics: The inherent complexity of robotics presents challenges, including reliability and stability concerns in varying conditions.
Staffing and Danger: Automation mitigates staffing challenges in hazardous or remote environments but does not alter the inherent dangers associated with such applications.
Understanding these limitations is crucial for informed decision-making. Consulting directly with Polymath Robotics can provide clarity on how these factors may impact specific use cases.
How does polymathrobotics.com address safety concerns in hazardous environments?
Polymath Robotics prioritizes safety in hazardous environments through various measures:
Safety-Critical Navigation: Integrates safety-critical navigation features to ensure the autonomous operation remains safe, even in hazardous conditions.
Robust Sensor Integration: Supports a diverse range of sensors, including those designed for hazardous environment detection like thermal, gas, and radiation sensors.
Advanced Algorithms: Utilizes advanced algorithms for object detection and path planning, crucial for navigating safely in unpredictable environments.
Redundant Systems: Likely implements redundant systems for critical functions, ensuring continuity of operation even if one system fails.
Safety Protocols: Adheres to industry-standard safety protocols and best practices to mitigate risks associated with autonomous machinery.
Continuous Monitoring: Designed for continuous monitoring and real-time adjustments to respond to dynamic changes in the environment.
Collaboration with Experts: Collaborates with robotics and autonomy experts to uphold high safety standards.
Customization for Specific Environments: Offers customization options to tailor the system to specific environmental challenges and safety requirements.
For comprehensive insights into how Polymath Robotics addresses safety in hazardous environments, direct consultation with their technical team or reference to their official resources is recommended.
What types of industrial vehicles can Polymathrobotics automate?
Polymathrobotics specializes in automating a variety of industrial vehicles used in off-highway environments. Their system can be integrated into agricultural vehicles, mining equipment, ground support equipment, yard trucks, forestry equipment, and earth-moving equipment. The system's vehicle-agnostic nature allows it to adapt to the unique dynamics of different vehicles operating in these sectors, making it a versatile solution for enhancing operational efficiency and safety.
How do Polymathrobotics' autonomous navigation modules enhance industrial operations?
Polymathrobotics' autonomous navigation modules are designed to supercharge industrial operations by allowing teams to add safe, autonomous navigation to vehicles. This alleviates the need for a driver while ensuring safety is maintained, facilitating a focus on completing meaningful tasks. The system streamlines the path to autonomy by providing a mature vehicle dynamics model, reducing the need for frequent interventions and lowering network bandwidth requirements, ultimately enhancing productivity and operational efficiency in controlled environments.
What flexibility does Polymathrobotics offer for industrial vehicle automation?
Polymathrobotics offers remarkable flexibility for industrial vehicle automation through its vehicle-agnostic and compute-agnostic technology. The system is compatible with most sensors and can be commanded via an API, enabling seamless integration with existing software frameworks. This flexibility is particularly beneficial for operators looking to automate large industrial vehicles in contained, off-road environments without the need for extensive hardware modifications, allowing for swift and cost-effective deployment of autonomous capabilities.